Guillaume Halleux has a unique overview of the air cargo market having worked across various sectors. Now he is applying that experience at Swissport.
Last year Guillaume Halleux left his role heading up the cargo team at Qatar Airways to join ground handler Swissport as chief commercial officer.
The move means he now has a unique overview of the cargo market, having worked for airlines, a handler and a forwarder in the shape of Bolloré Logistics.
Explaining his decision to leave the top job at the world’s largest cargo airline, he says his thinking was two-fold.
Firstly, he wanted to re-locate to be closer to his ageing parents and secondly, after 25 years in airfreight, he felt it was time to try something a bit different.
“So, here I am in the beautiful world of ground handling,” he says. “At Swissport, I found a very nice team that are dedicated to the job they do, so that part is really enjoyable. And, I was welcomed with open arms and I am really enjoying it.”
Halleux says the main difference between a cargo airline and a ground handler – other than the obvious lack of flying – is the centralised operations of the latter.
Handlers have facilities dispersed across the world which creates the challenge of trying to provide a uniform standard of service throughout the network.
Swissport employs 60,000 people globally, with only around 50 of these based at the head office.
Airlines on the other hand are controlled centrally with head offices “very heavy in terms of people”.
“At Swissport, each region has its own management and the role of the head office is to guide and steer as well as control internal compliance,” he says.
“We act as support to the regions and we also act to safeguard the sustainability of the business, so that is a massive difference. And it takes a learning curve.”
Halleux says that before joining Swissport he viewed handlers on a station-by-station basis, explaining that different facilities in neighbouring countries could provide different standards of service.
So how does Swissport tackle this challenge?
“Consistency is key and we have rolled out a number of initiatives to ensure that consistency,” says Halleux.
“For example, every station has the same scorecard, our stations have the same manual to follow, the operating procedures are standardised, on the cargo side we only use one system, Cargospot, and it is the same version of the system everywhere to ensure consistency.”
People challenge
One of the main challenges faced by cargo handlers in recent years has been attracting labour following the Covid pandemic where many people left the industry due to the shutdown of aviation and opted not to return, taking other service jobs away from the airport instead.
Firms with a large cargo department, such as Swissport, were able to avoid the worst of the issues when it came to re-recruitment because the surge in air cargo at the height of the Covid pandemic – and the complexity of handling cargo due to unpredictable airline schedules and needing to take cargo out of the cabin of aircraft – meant many staff were kept on.
However, Swissport itself is not immune to the issue and in some locations, Japan for example, the company has an agreement with the country’s government that allows it to bring in manpower from other countries because “we cannot find locals” and it is “not the only example”, Halleux says.
Halleux adds that a related issue has been a surge in wages due to inflation and fewer members of staff across the industry as a whole.
Labour is therefore a key area of investment for Swissport.
“The headcount is heavy because that is what we do for a living, we provide people to turn aircraft, to palletise cargo, to handle cargo, so we aim to be an employer of choice
“Labour is absolutely a strategic element of our business, which we have to control properly to attract talent, retain talent, to train people.”
He says that the company has rolled out a number of initiatives to help make the company an attractive place to work.
For example, Swissport has committed to provide staff rosters one month ahead of time so that people can plan their personal lives around their shifts.
He says that in handling it is not rare people get just a few days’ notice of their upcoming shifts… “how do you plan your family life,” says Halleux.
‘Allowing your team to plan their lives’ is one of the six Red Rules that Swissport has committed to as a minimum standard for every station.
Other Red Rules are: pay a fair wage; create a safe space to recharge; give people reasons to be proud of their job; ensure competence and confidence; and share the workload.
Other cargo investments include adding new warehousing facilities.
“We operate 130 warehouses around the world, which is not a small number, and that is really the name of the game,” Halleux says.
“The minute we see a warehouse opportunity somewhere we reach out for it as much as possible.”
The handler is currently in the process of opening new warehouses in Melbourne, Manchester, Zaragoza and London Heathow.
“All of those are fresh developments that illustrate our hunt for warehouses to be able to better serve our customers,” he says.
Halleux says there are gaps in its maps where Swissport would potentially like to add facilities, but the actual process is more opportunistic.
“We are just always on the lookout,” he says. “So we do it the other way round - we look everywhere and if there is an opportunity we assess it.
“Sometimes we say no, but it is very rare because they don’t come very often, so you have got to be quick.”
Airline demands
The aviation market has changed rapidly over recent years as a result of the Covid pandemic and Halleux says this has brought about demand for greater productivity through digitalisation and automation.
“We are investing in a number of solutions to automate as much as possible,” he says. “For example, we are a launch customer of Cargospot-neo (the latest iteration of the cargo handling software) and actually helped co-design the product.”
Cargospot-neo supports a high level of automation across many handling processes.
Not least, says developer CHAMP, with the “most advanced set of mobile applications available”, it will enable Swissport to achieve 30% efficiencies in its warehouse operations.
Cargospot-neo has in-built machine learning (ML) and artificial intelligence (AI) technology.
It has three new service modules: Task Manager, Customer Portal and Mobile Service Point.
Task Manager enables a ‘steering’ process whereby terminal resources can be directed to perform tasks or execute instructions through mobile devices and other means.
The Customer Portal builds on the pre-existing Cargospot Portal but introduces zero-touch processes that are specific to cargo terminal operations.
And the Mobile Service Point functions as a ‘virtual kiosk’ to provide support for customer zero touch processes typically performed at a cargo terminal, without the cost or space requirements of fixed kiosk terminals.
Halleux adds that the company has also been working closely with Airbus on the development of its Airbus A350 freighter.
“We work with aircraft manufacturers to integrate the handling of the aircraft into the technological enhancement of the aeroplane,” he says.
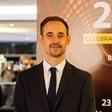